Omrörare: En Nödvändig Komponent inom Industrin
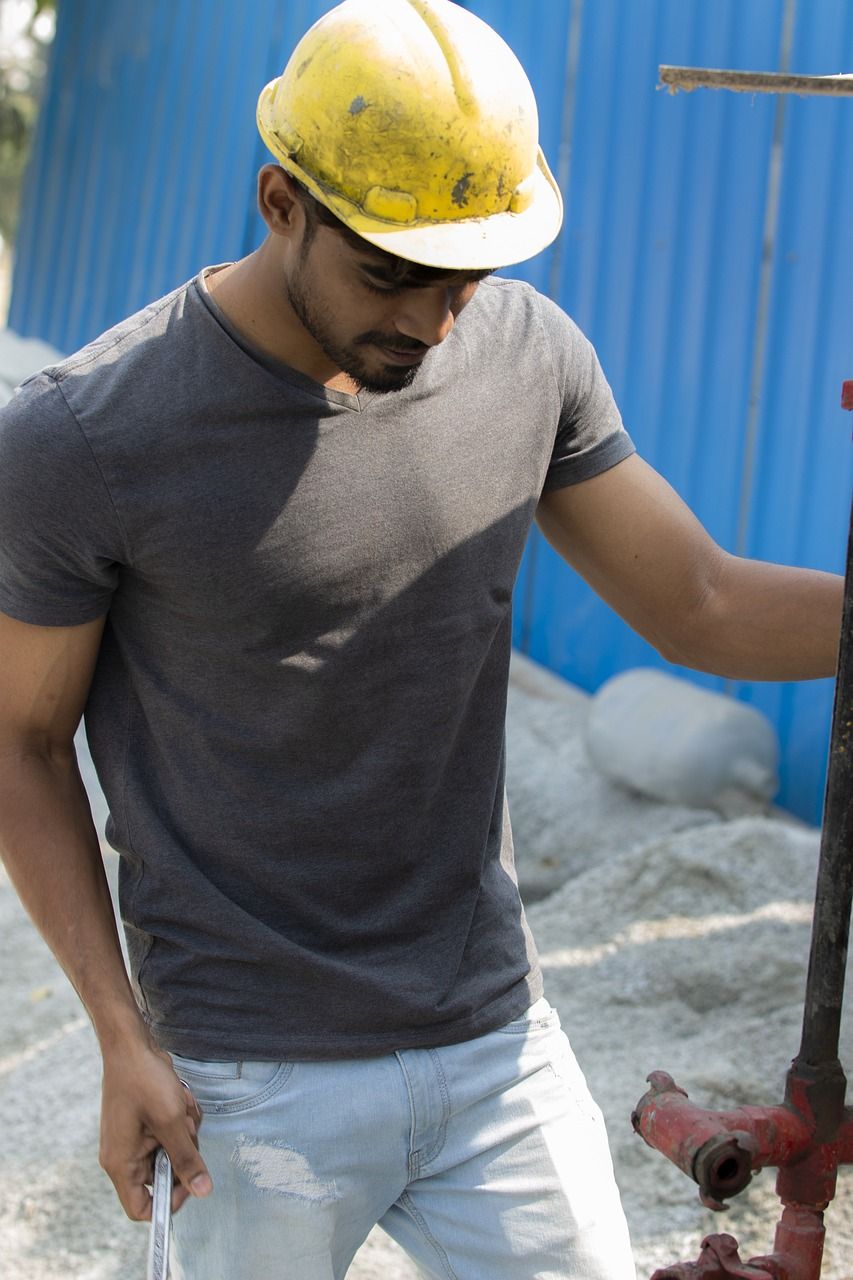
Omrörare, även kända som blandare eller agitatorer, är en kritisk utrustning inom ett flertal industriella miljöer, där de används för att säkerställa homogenitet och effektivitet i processer som involverar vätskor, gaser och även fasta partiklar. Denna artikel går igenom olika aspekter av omrörare, deras funktion i diverse tillämpningar och vad tillverkare bör överväga när de väljer den rätta omröraren för sina processbehov.
Grundläggande Principer för Omrörarteknik
Omrörare utgör ryggraden i många processindustrier, inklusive kemisk tillverkning, läkemedel, livsmedelsproduktion och vattenbehandling. En omrörare är utformad för att skapa en kontrollerad rörelse i en vätske- eller suspensionsmassa för att uppnå önskad blandning. Denna rörelse möjliggör viktiga processer såsom homogenisering, värmeöverföring, massöverföring och gasdispersion. För att effektivisera dessa processer, måste omröraren vara noggrant utvald baserad på blandningstid, effektivitet och avsedd användning.
När man talar om omrörarteknik, blir det vitalt att förstå de mekaniska och fluidmekaniska egenskaperna hos systemet. Omrörarens design, inklusive form och typ av blad, axel och drivsystem, är avgörande för att kunna generera en fördelaktig strömningsprofil och skjuvkraft för att blanda komponenter effektivt med minimal energianvändning. Principer som Reynoldstal, Froudes tal och powersamband spelar en viktig roll i karaktäriseringen och optimeringen av omrörarens prestanda.
Typer av Omrörare och Dess Tillämpningar
Tillverkare stöter på en mängd omröraralternativ beroende på deras specifika processbehov. Dessa kan kategoriseras i två huvudtyper: rotationella och reciprokerande omrörare. Rotationella omrörare använder sig av en centrerad axel med fasta blad som roterar för att skapa strömningsmönster. Dessa blad kan vara av olika geometri, som till exempel propeller, turbin, padel eller ankartyp, beroende på applikationens viskositet och blandningsmål.
Å andra sidan skapar reciprokerande omrörare en upplyftande eller pulserande rörelse med hjälp av en kolv eller diafragma. Dessa är idealiska för applikationer där skonsam men effektiv blandning krävs eller där vätskans viskositet är mycket hög.
Varje typ av omrörare tillgodoser särskilda processkrav. Exempelvis är propellertypen omrörare effektiv för lågviskositetsmedia och snabb blandning, medan plogbladsmixrar är mer lämpade för tunga och viskösa blandningar. För suspensioner av fasta partiklar kan en helikalbandblandare vara optimal då den både blandar och transporterar materialet i processkärlet.
Utformning av Omrörare och Optimering
Effektiva och pålitliga omrörare beroende på deras utformning. Det innebär en ingående förståelse för både de processparametrar som verkar i systemet och materialegenskaperna hos de substanser som ska blandas. För att säkerställa optimal produktkvalitet och processprestanda är det nödvändigt att anpassa omrörarens design till applikationens specifikationer. Detta inkluderar att utvärdera bladgeometri, axellängd, rotationshastighet och utformning av kärlet.
Tillverkare måste också beakta faktorer som skalbarhet, energieffektivitet och underhållskrav. Det är ofta effektivt att genomföra laboratorie- eller pilotskala tester för att simulera och verifiera blandningsprestanda innan en fullskalig implementering genomförs. Avancerad modellering och simulering, som Computational Fluid Dynamics (CFD), kan ytterligare bidra till att optimera omrörardesignen för en given process.
Val och Underhåll av Omrörare
Slutligen är det avgörande för tillverkare att noggrant välja rätt omrörare och underhålla dem korrekt i syfte att maximera processens livslängd. Matchning av omrörarkapaciteten med processkraven är inte bara avgörande för processresultatet utan påverkar även ekonomiska och operativa aspekter. Rätt val underlättar en effektiv användning av växelströmsmotorer och minimerar överflödigt slitage.
Regelbundet underhåll och inspektion av omrörarsystemet är nödvändigt för att förhindra produktionsstopp och utrustningsfel. Kontroller av axeltätningar, lager, och bladmekanism ska utföras i enlighet med tillverkarens rekommendationer. Att investera i kvalitativa material och komponenter kommer initialt att vara dyrare, men över tid minskar det totala kostnaderna genom minskad driftstopp och ökad anläggningsprestanda.